FY6900 OCXO - 30.05.2024
Once you've started to experiment with radio transmitters and receivers, you quickly end up at a point, where you need a known good signal source for testing.
You can usually get a slightly used, but working, HP 3312A for 300€ on eBay. I'm not joking. I wish I was. At the time of writing these fully analogue function generators, that were all build decades before I was born, go for nearly the same prices as e.g. the modern Siglent SDG1032X.
So let's not do that. Instead, you can just wait until somebody drops three broken 3312As into your lap and subsequently spent many evenings nursing those amazing, but thoroughly confusing analogue artworks back to health. I even got two of the original manuals in mint-condition.
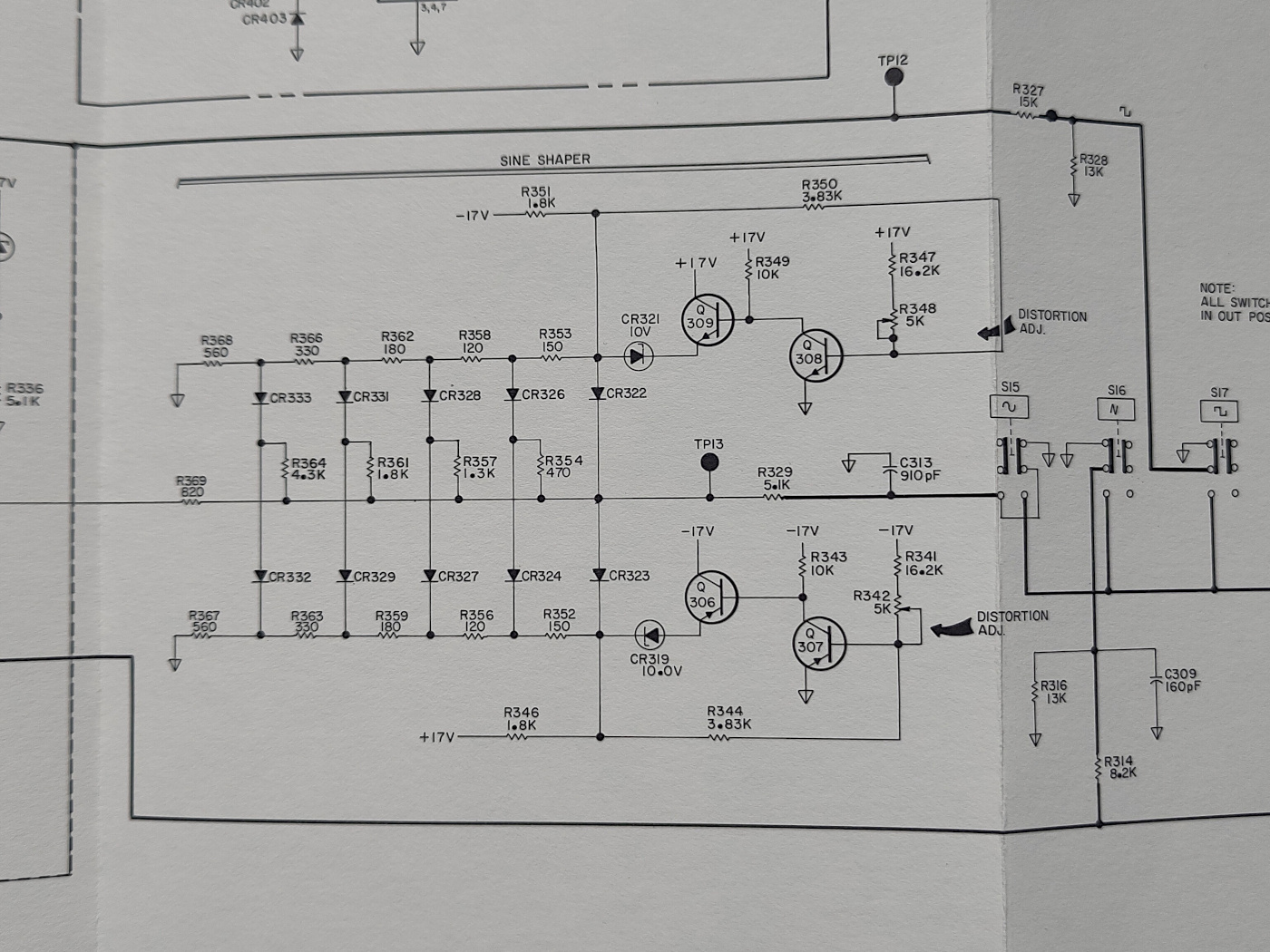
While those old instruments can usually be repaired by replacing some basic worn-out discrete components, and doing so apparently makes for a great CuriousMarc video, I wouldn't necessarily recommend that route. (That is unless you fancy spending a half a night wondering what drugs they were handing at HP back in the day.)
So you should get the Siglent. That would be expensive but reasonable, and it would just work.
Or... hear me out on that... you could head over to AliExpress or eBay and a get a FY6900 to modify it. It will cost you less than half of the Siglent. After making some minor improvements to it, it will hopefully still be cheaper but just as nice as the proper one.
Let me level with you: I don't have to justify myself for going straight for the hacky solution. I had a bigger project to procrastinate and procrastinate it I did. No yak shall go unshaved. Furthermore, I would like to remind you, that you dear reader clicked on this article about hacking a cheap Chinese instrument, so you are probably in no position to judge.
So I got one from AliExpress. Fresh out of the box the performance is okay..ish.
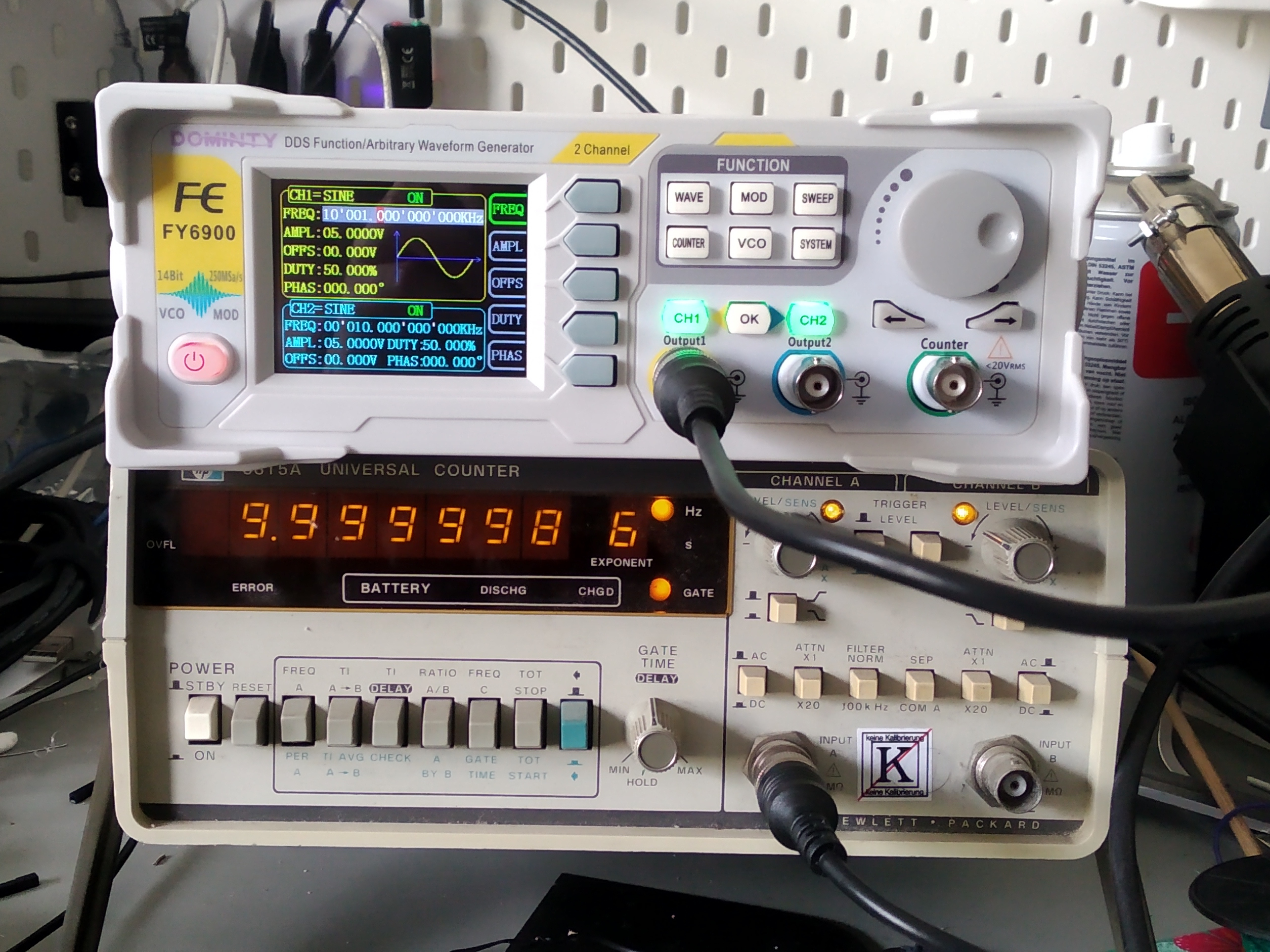
It could be a lot worse. Only 1kHz off according to the counter that has last been calibrated over 20 years ago.
Pretty sure there is some compensation for that in some Menu.
After messing a little bit with the OSCI
-Setting and trying the spectrum analyser instead of the counter,
because it has been calibrated in this decade, the generator appeared fairly spot on.
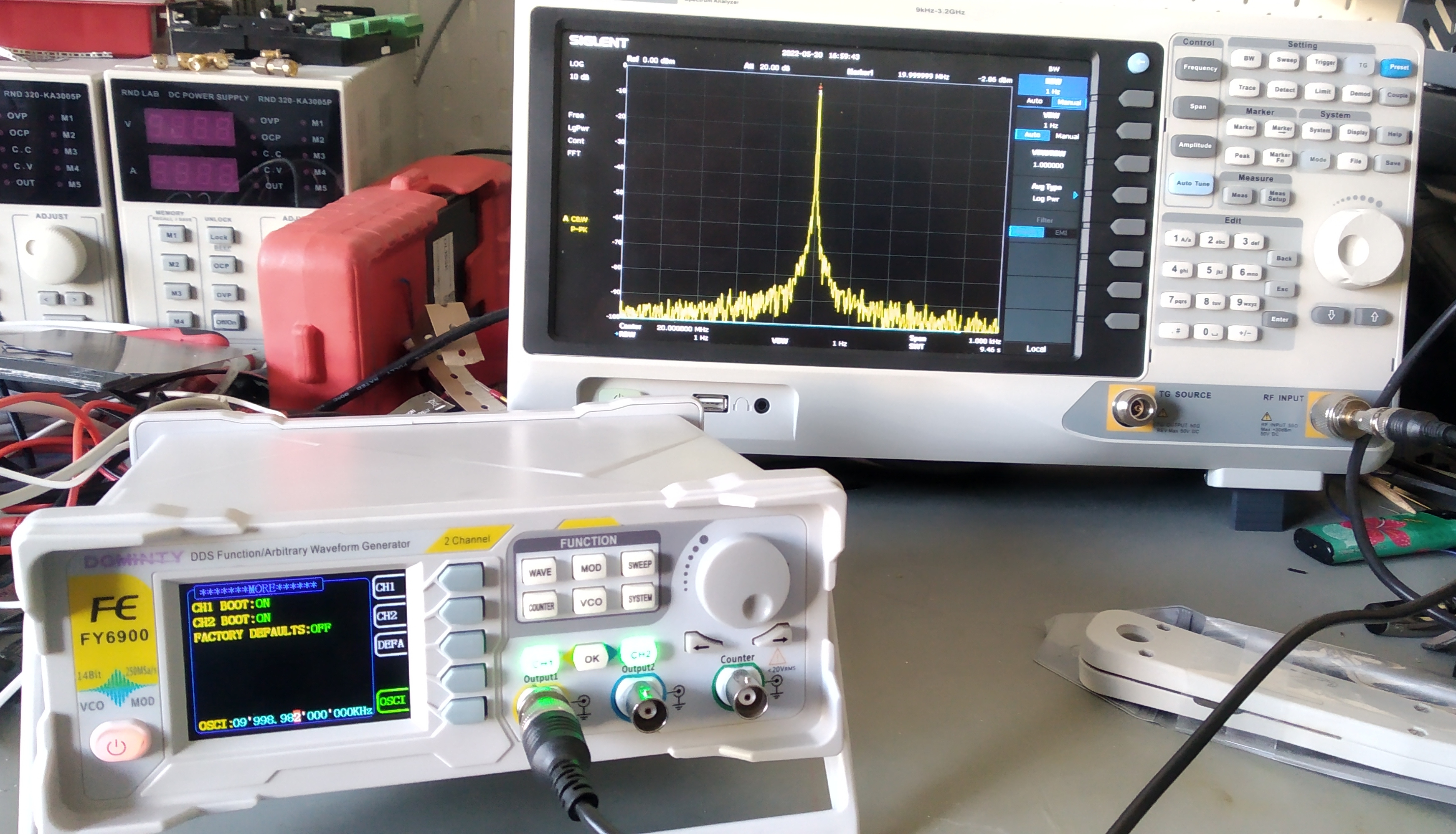
Sine setting is reasonably clean, it has decently low harmonics and a lot less weird sidebands,than I expected. Until I opened the window, and it started wandering all over the place. The temperature stability is basically non-existent. Fortunately this is something that can be fixed without too much effort.
So let's take a look inside. There is one central screw in the bottom of the unit. After undoing that, the front and back can be unclipped and finally the upper half the housing can be lifted away.
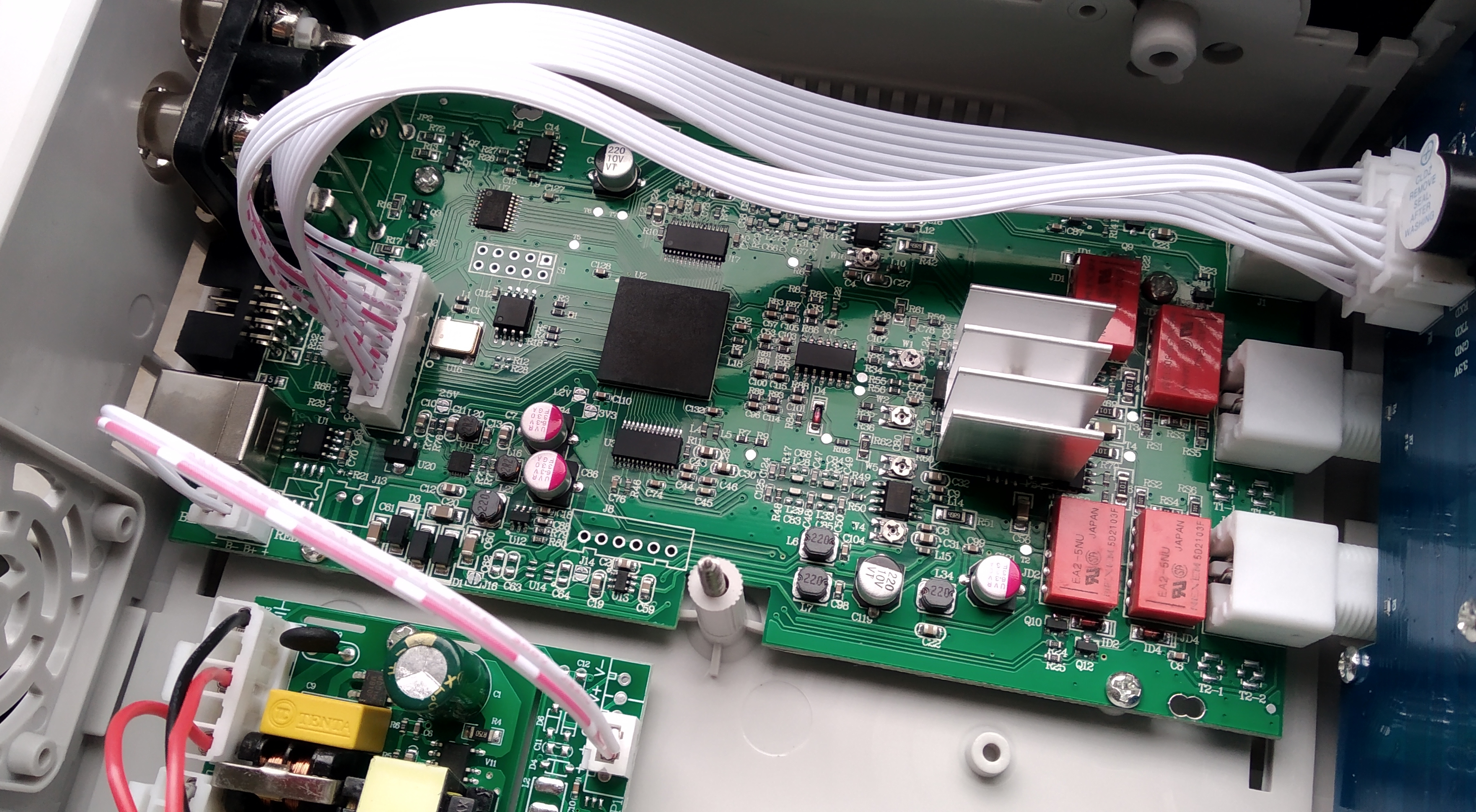
And here's our problem. Right next to the cable connecting to the display PCB is a small, probably cheap, crystal oscillator, just hanging out in the breeze of the non-existing cooling fan. A quick prodding with an oscilloscope revealed that it outputs a 10MHz rect with a maximum voltage of 3.3v. I just so happened to have something else that outputs a 10MHz rect, although it used a 5v level signal. Also, it didn't fit on that SMD footprint.
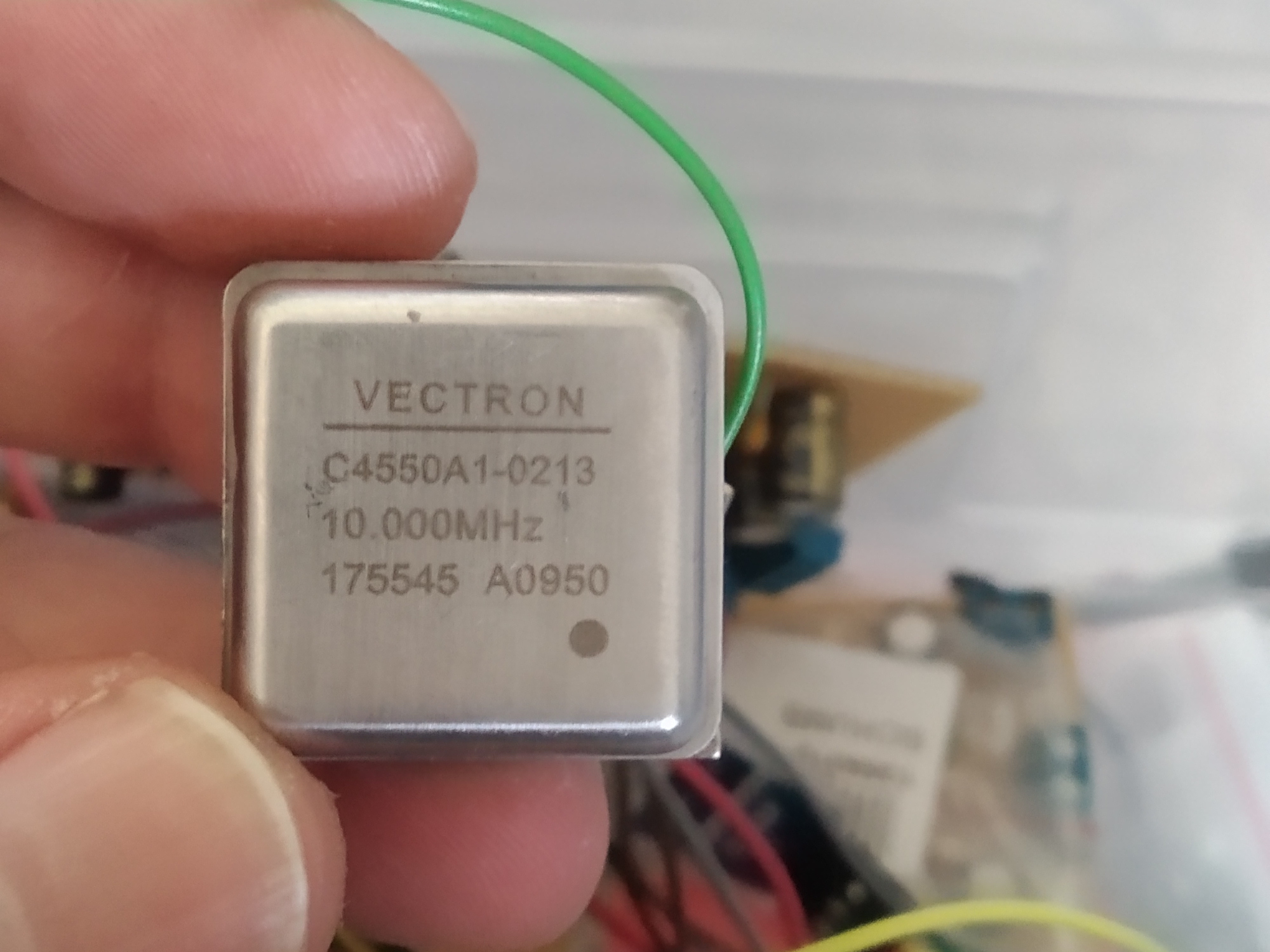
The Vectron C4550A1-0213 has been used in a lot of networking and telco equipment, which now gets slowly phased out. This means there is steady flow of slightly used surplus oven controlled crystal oscillators into your favourite online marketplace. You can usually pick them up slightly dented for less than 10€ with bits of the original PCB still attached. Over the years I bought about 10 of them from different places, and so far they all worked and were within spec.
I quickly put one on a piece of perfboard, together with a U74HC14L
that acts as Schmitt-trigger for signal conditioning,
as well as a buffer to decouple the OXCO output from capacitive load and a level shifter from 5v to 3.3v output.
There is just enough unused space behind the power supply to perfectly fit this board.

The original oscillator was unsoldered carefully using a hot air. After that it is relatively straight forward to solder a piece of micro coax to its pads.

Fortunately, you can steal 5v and GND directly from the power supply output pins, there are even some unused solder pads prepared for you. 3.3v is a little more tricky. The cleanest solution I found was to solder to the 3.3v pad of the front panel connector. First tests with this new prototype were promising, the frequency was a lot more stable. It was also consistently off by the same few hertz after powering off and on again (and giving the oven some time to warm up of course). Since I didn't have an actual frequency normal at hand I decided to tune it to the reference of my spectrum analyser.
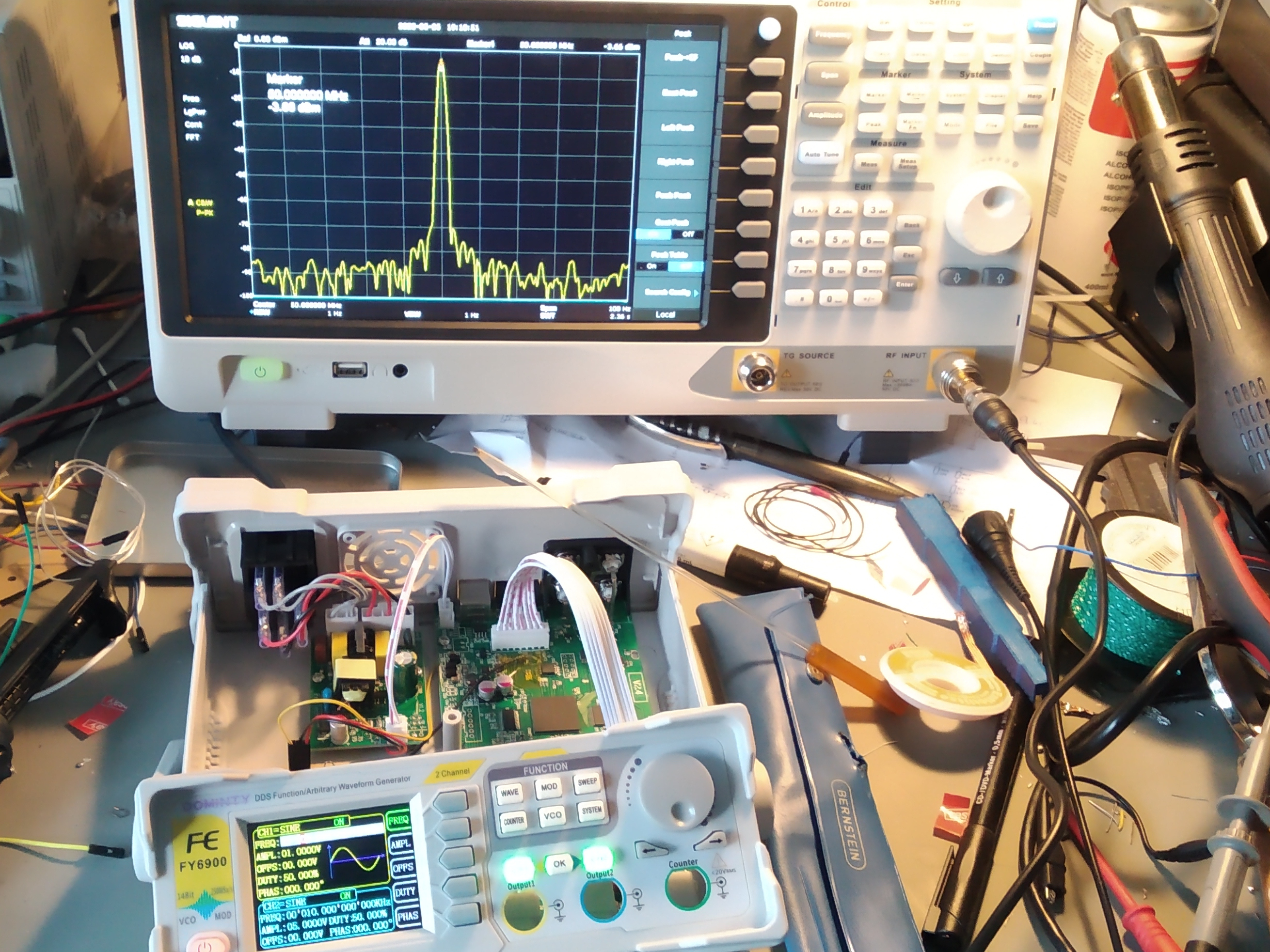
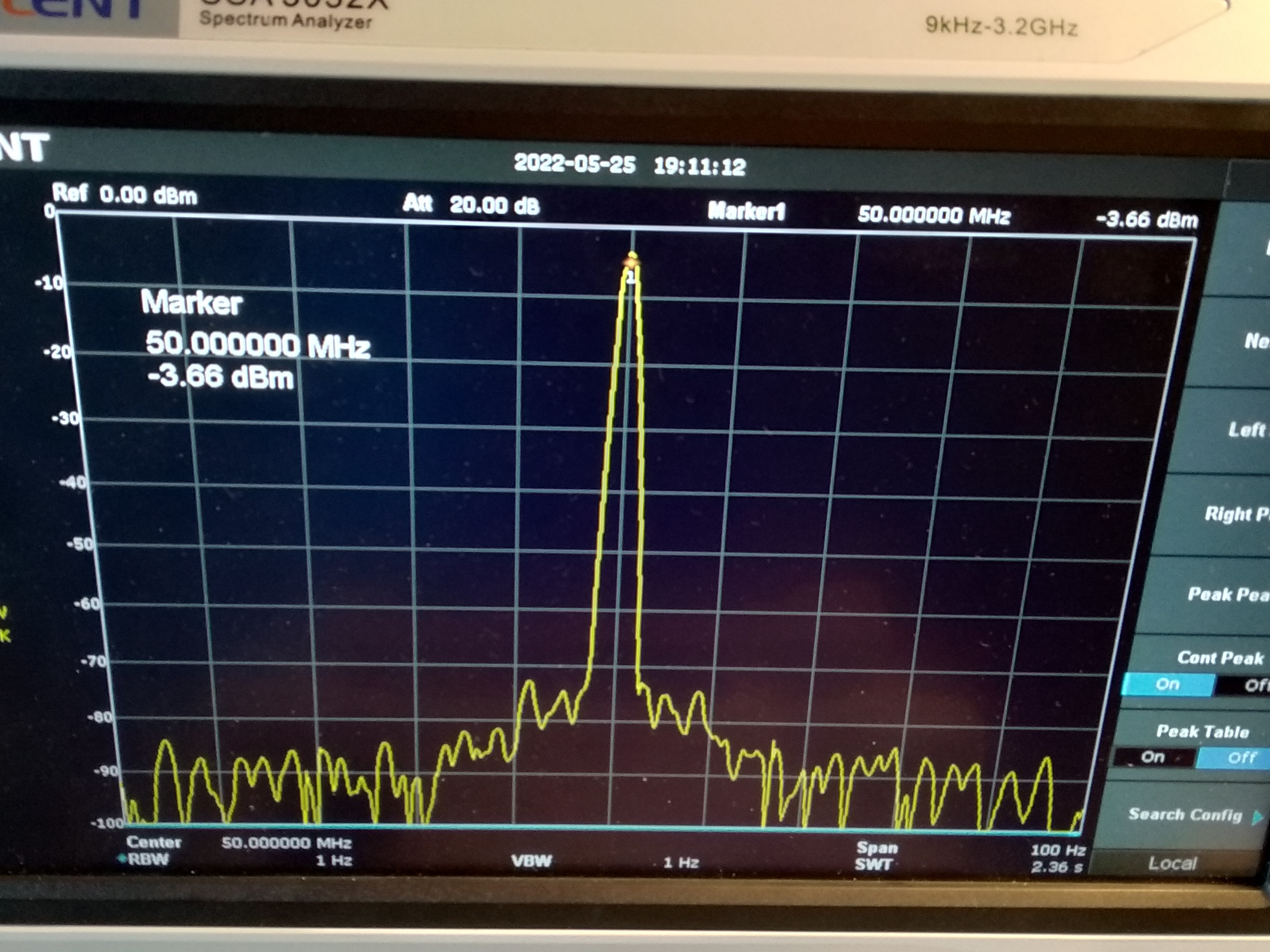
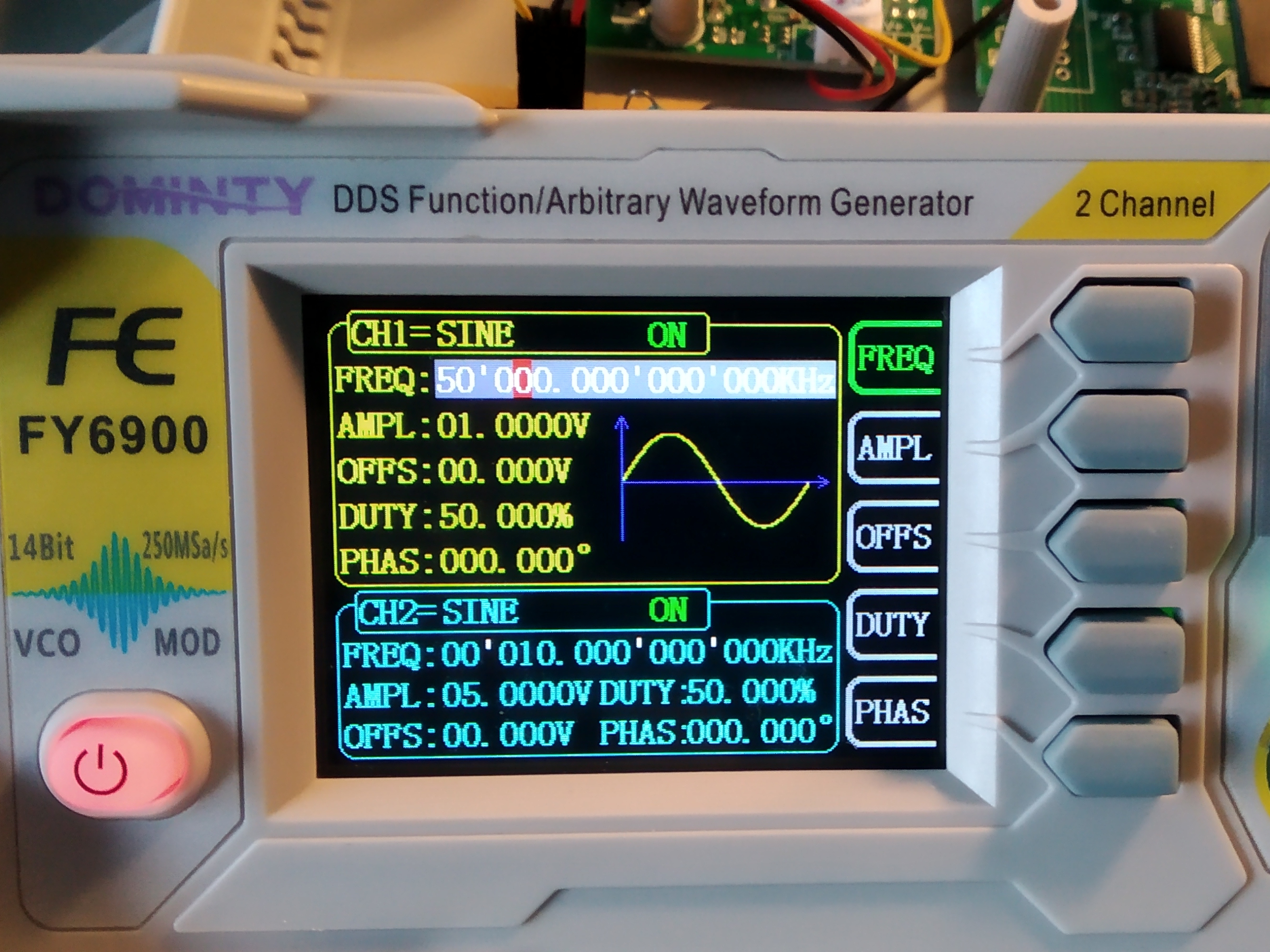
Unsurprisingly tweaking the trimmer potentiometer with a metal screwdriver is not the best idea. The screw of the trimmer is connected to one of the contacts and attaching a bit of conductive material, also known as screwdriver, to it, is effectively attaching an antenna to the to OCXOs frequency tuning pin. In the best case I would only get some weird sidebands that made it through the PLLs into the output signals. In the worst case the signal would be exactly on frequency and run away as soon as the screwdriver was removed. As a workaround you can use the little plastic screwdriver that you got with oscilloscope probes. Or if you are feeling fancy, like I did, break out the fancy plastic screwdrivers with ceramic blades.
Now that the prototype was working, I could continue to build a "proper" OCXO add-on board.
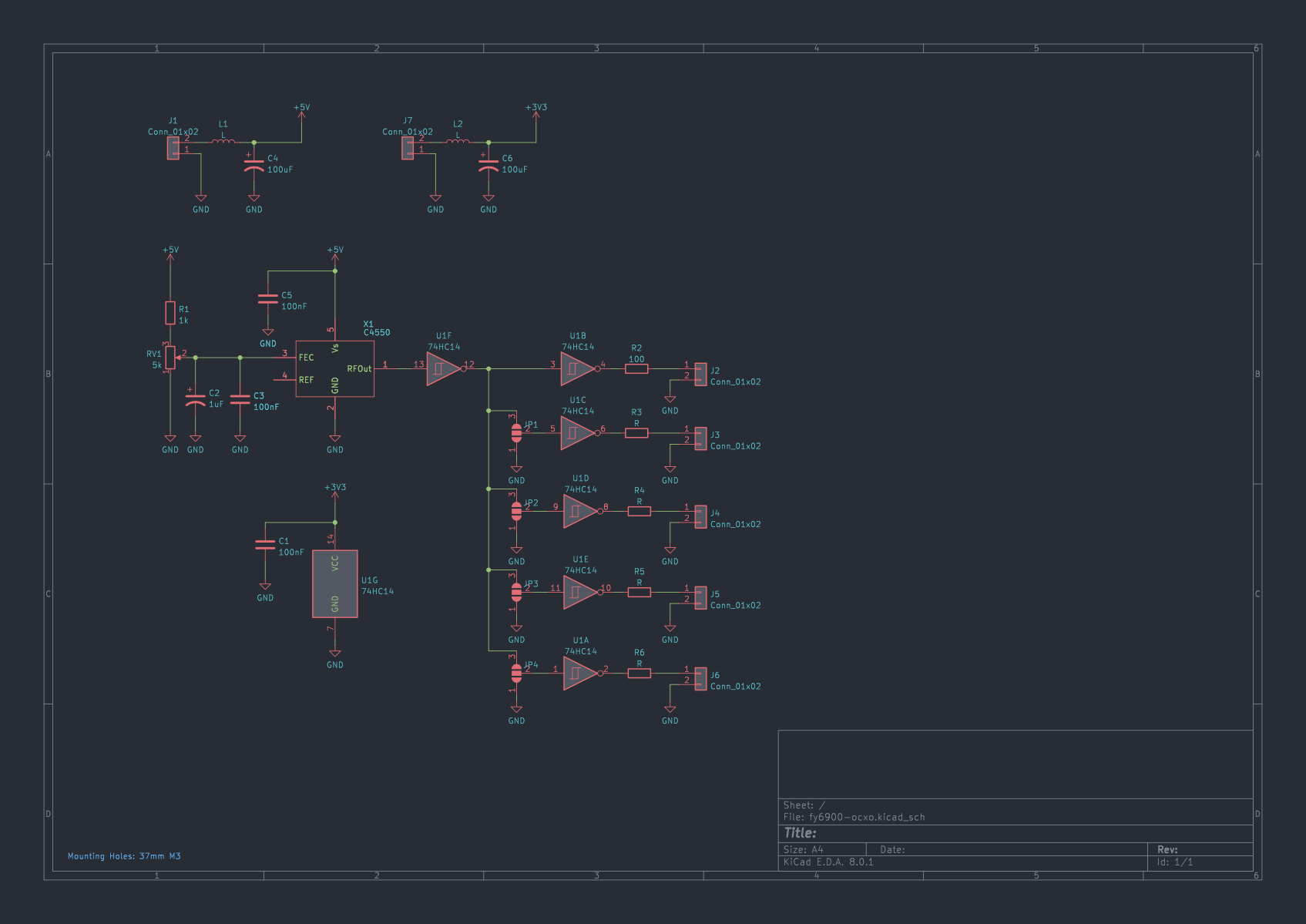
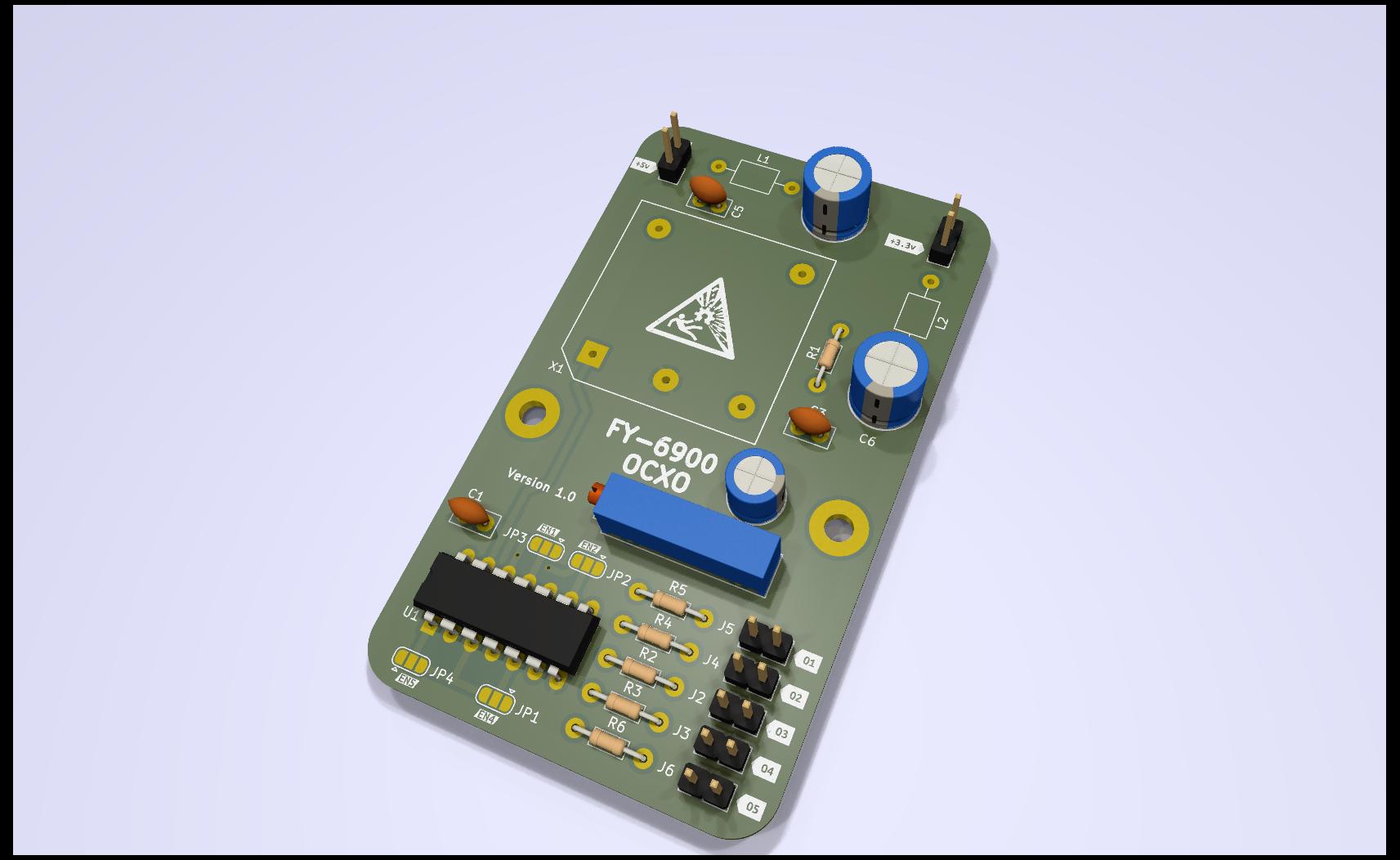
If you are interested in the gerbers or the CAD files, I've recently updated all the files to KiCAD 8 and uploaded it to my forgejo instance: forgejo.zenerdio.de/sebastian/fy6900-ocxo.
It is pretty much the same thing as the perfboard prototype. It has an input header for 5v and 3.3v. Both voltages are filtered using a series inductor and parallel capacitor. I chose 1uH and 100uF pretty much because that's what I still had leftover from another project. Exact values aren't too critical here, all those filters do is keep higher frequency stuff from the generator sneaking in the OCXO output and vice versa. As far as I can tell, those values work reasonably well for this. However, keep in mind that I've never actually done any measurements to verify of that. It's a lot of work to do properly, and the output looks fine, so either it works as intended, or there never as an issue to begin with.
The frequency error correction pin of the C4550A1 is attached to the centre tap of a multi-turn trimmer and a 1uF as well a 100nF to ground. I wanted to be extra sure that the voltage at this pin is as stable as possible, regardless of what's happing on the power rails. It might be worth adding a some form of voltage reference (z-diode, actual voltage reference chip...), but then again this is an add-on to a cheap little function generator, not some high precision GPS-disciplined reference oscillator. Keeping it from producing weird side tones in the generators output is probably enough.
The signal conditioning is still handled by a 74HC14. The first Schmitt-trigger unit turns the output of the OCXO into a clean rectangle signal. After that the other units are abused as distribution amplifiers. Having more than one output allows to use the board for other things as well, as the PCB-factory sends you 5 or 10 boards anyway and I don't plan on converting more than one cheap signal generator. The inputs to each output stage can be connected to the first stage or ground via a solder jumper. Unterminated outputs oscillating at 10MHz turn the output stage into a transmitter, with lots of juicy harmonics. If the inputs were left floating, they would just couple to the signal on the pins next to it, likely resulting in some form of self oscillations. The series resistors in the output path allow for some basic impedance matching, should it be required.
The PCB also has mounting hole that exactly fit the unused posts that the signal generator manufacturer placed next to the power supply.
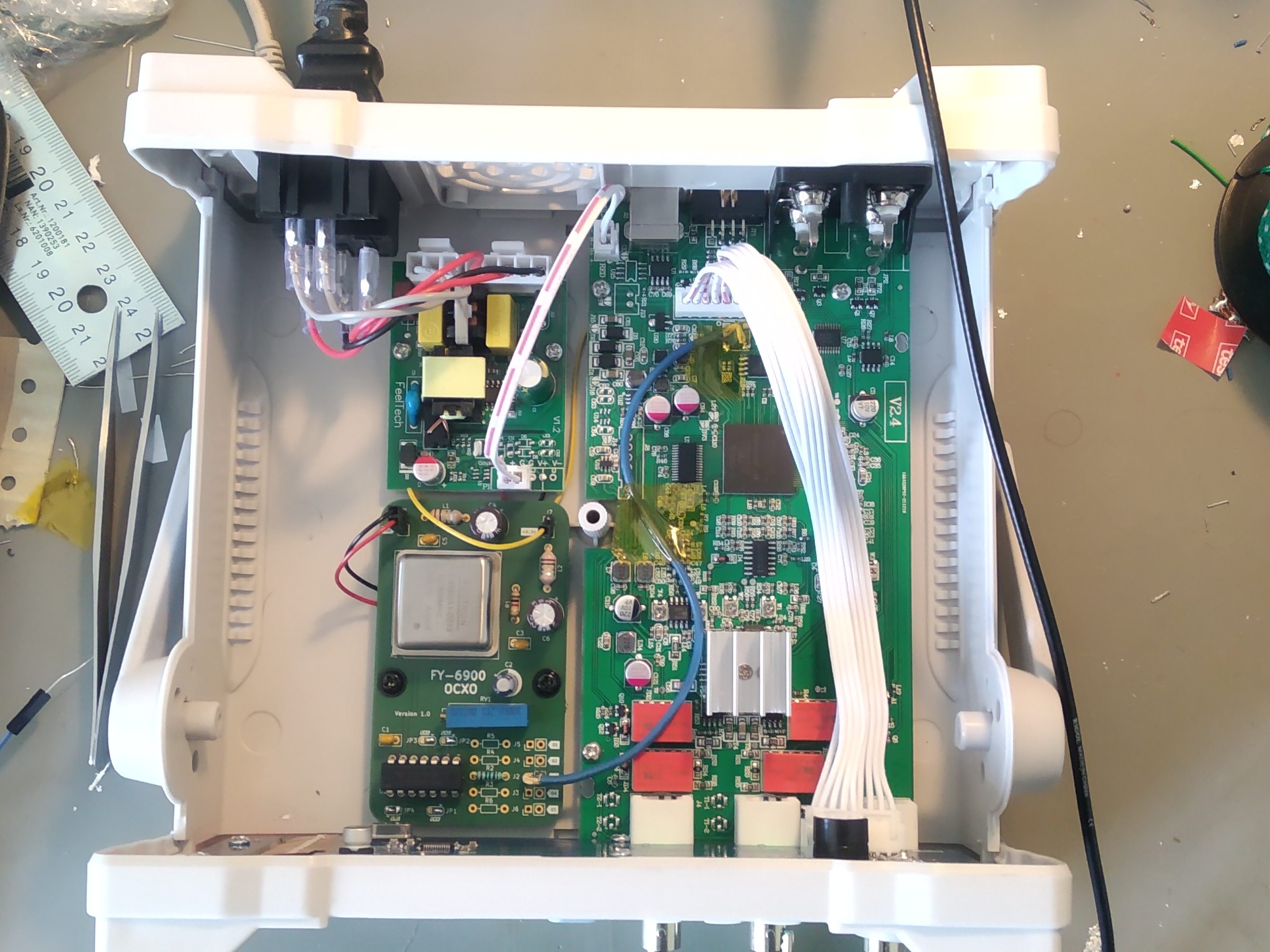
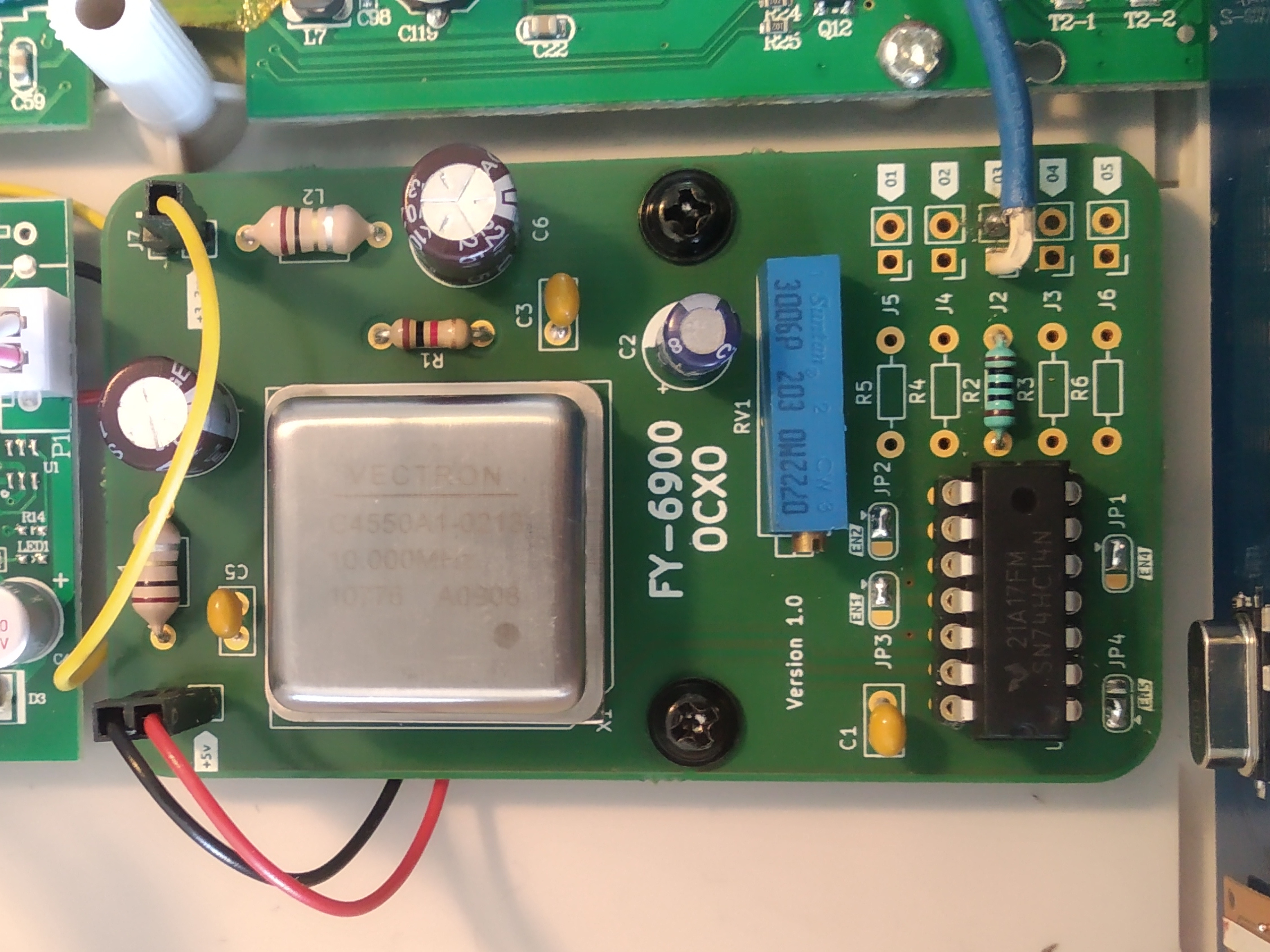
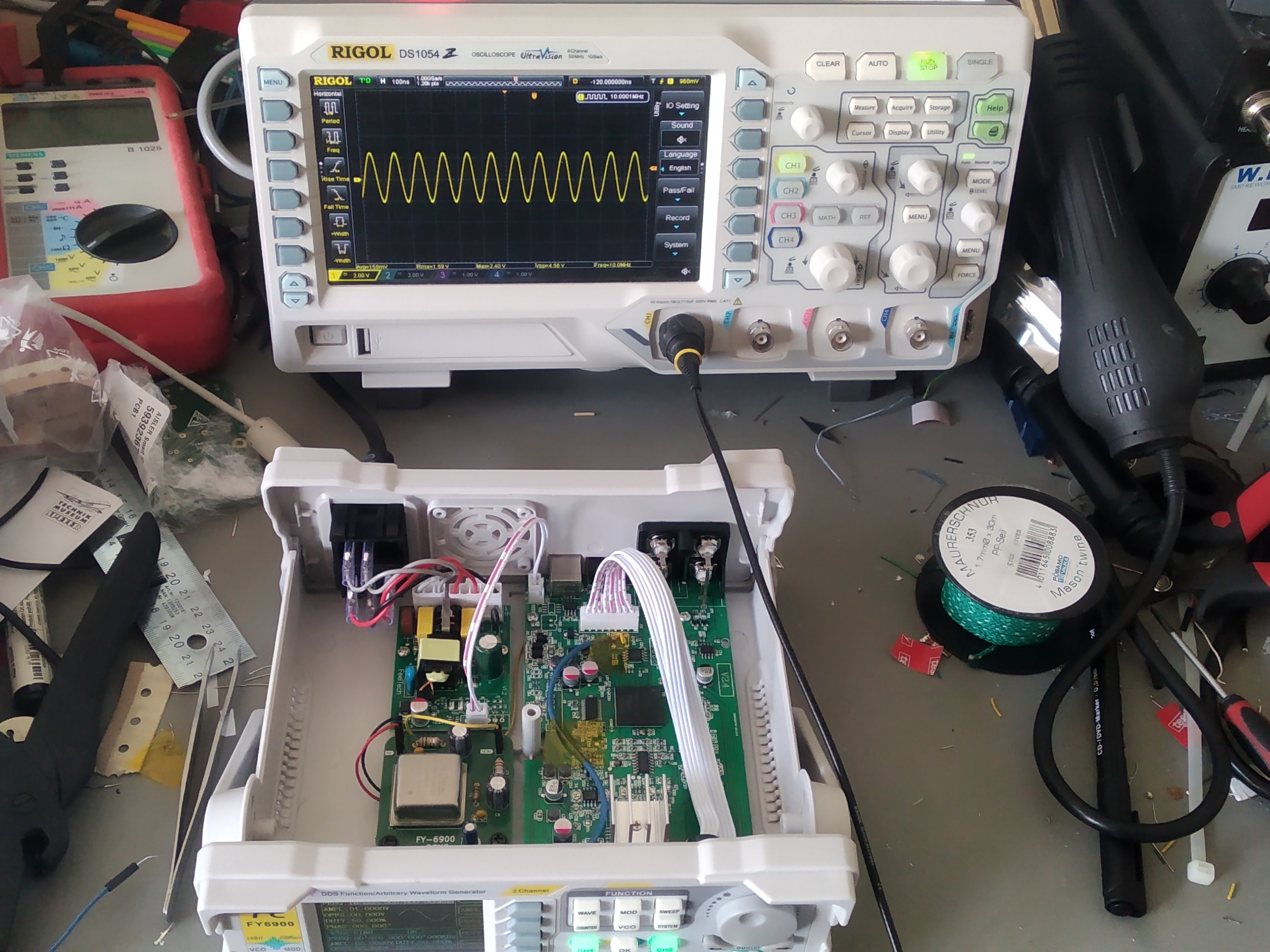
The final board also has the nice little tweak that the trimmer direct faces one of the holes that are covered by the handle. So it is possible (with some practise) to tweak the frequency after removing the handle without actually opening up the signal generator.
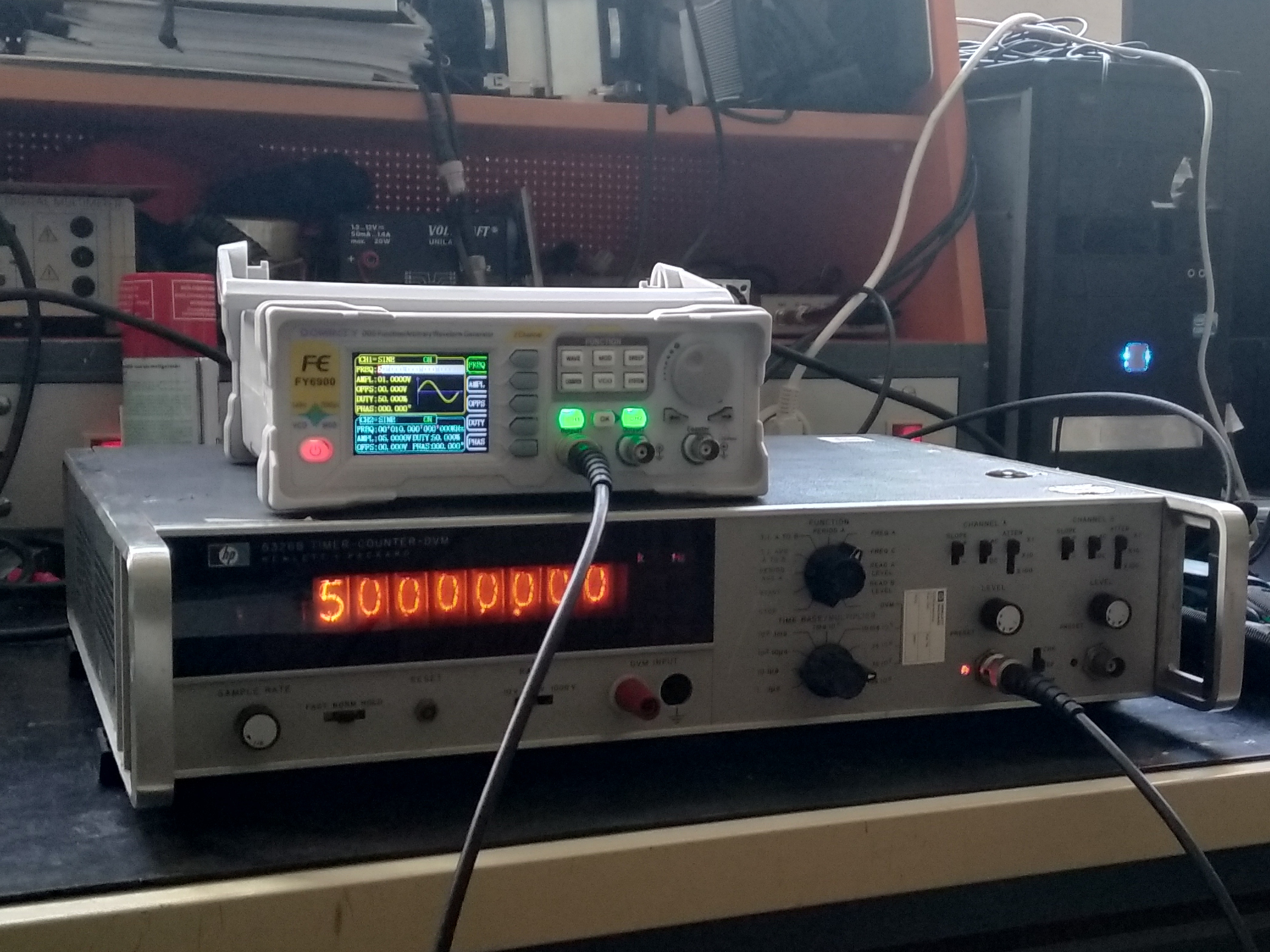
For the final frequency adjustment I needed a trustworthy source for a reference frequency. Back then we had a Trimble Thuderbolt in the DL0XK shack, along with a HP5326B frequency counter (those nixie tubes make all the difference). After some tweaking the FY6900 was spot on. More importantly it stayed that way even regardless of temperature. When I retested it a week later, it was still within +-1Hz at 50Mhz according to the GPSDO and the frequency counter. That's probably good enough for anything I'm working on at home.
One nice feature of the FY6900 is that you can load arbitrary waveforms into it via USB. The best tool I've found for that so far is fygen.
Using fygen and an old analogue scope, we can perform the final very important Correlated Amplitude Test, which critical for determining the performance of the upgraded unit.
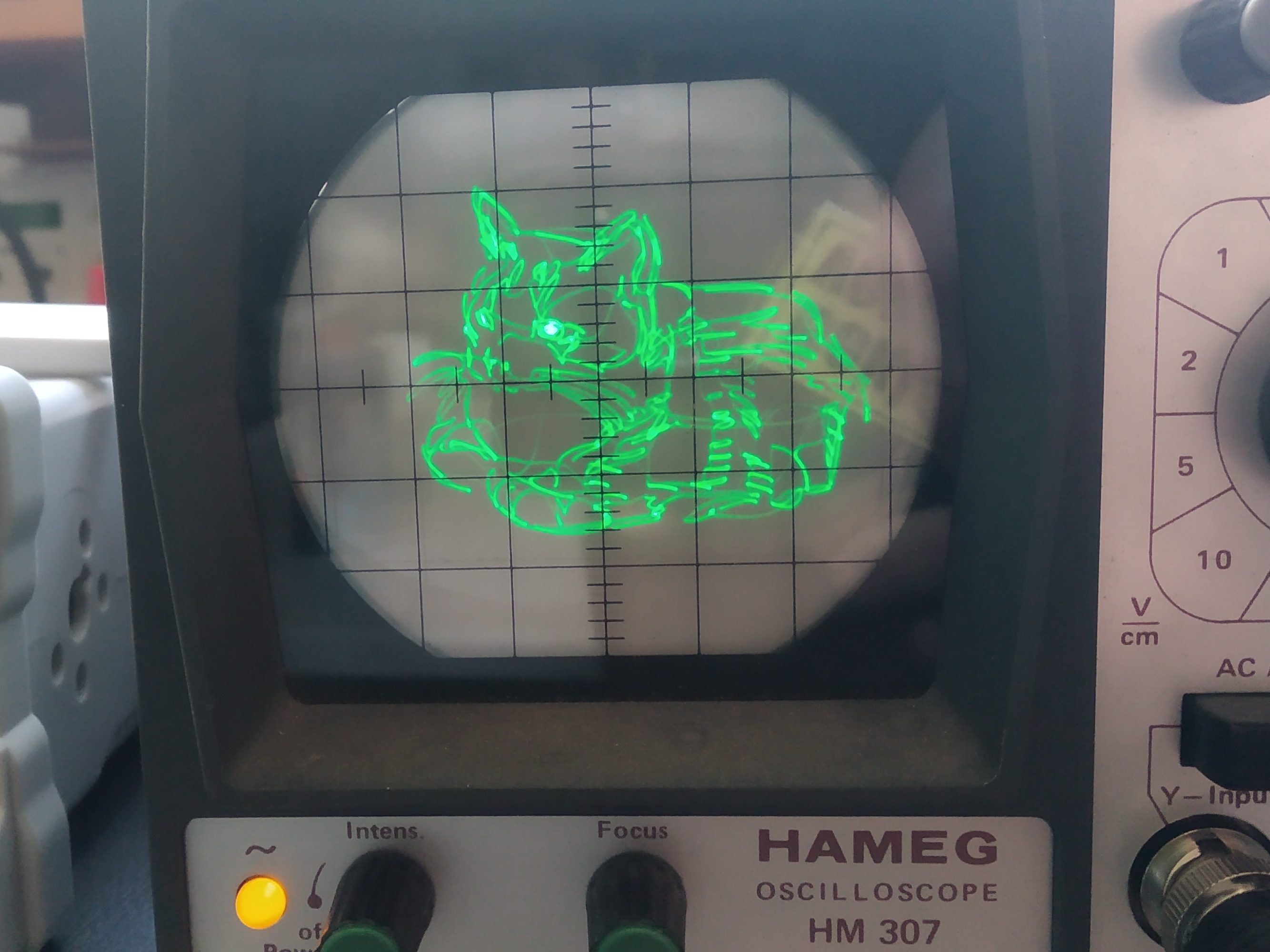
Semester Opening 2013 Poster - 26.07.2013
For those who don't know: Semester Opening is a big party organized by the computer science students council of the TU Kaiserslautern at the beginning of every summer semester. A month before the party z0ttel and I have been approached by the organisation team to add some special effects to the big poster, which was going to be put at the Mensa. The theme of this years posters and flyers was space and so they wanted sparkling stars on their poster. Of course we could have just gone to ebay and ordered some led powered blinkenthingies to clue at the poster, but where is the fun in this ?
As hardware hackers with a reputation to lose we decided to roll our own. We went for small microcontroller with one led at each IO pin, and some hacked together software pwm. Only a few ours later we had already ordered 6 Attiny2313, 60leds and some resistors. z0ttel sacrificed some network cable for the wiring and some protoboard pcbs, while I wend trough my parts drawer to find some capacitors.
A few days later we met in the workshop of Chaos inKL our local hackerspace. The soldering began. It took us at least twice as long as expected to put everything together, since the wire from the network cable broke all the time. Note for next time: Use a more flexible cable.
The software was written by z0ttle in the mean time.
It can be found in his Github repo. Also I blew up about half of our microcontrollers by powering them with false polarity .... big D'oh-moment. Luckily I had replacement at hand.
After a long day we felt dizzy from the solder fumes, but we had all 59 leds wired up to 6 controllers.
One led was already broken when we unpacked it and we did not order extra parts ... shit happens.
One day later we met at the university, where we found this awesome hand painted poster supported by a broomstick, a ladder, a chair and this ancient relict oft the pre-personal-computer era (a Dietz System 6000).
Ravinrabbid and Rouven started cutting holes for the led, while z0ttel and I were fixing broken wires (again).
A role of tape later every led was in place.
Some intermediate wiring porn ...
Since the backside of the poster were accessible for lot of people in the place, where the poster was put up, we decided to add some covers over the controller boards.
At this point we realized that the queues in the mensa were going to lead right behind the poster. Having hundrets of people passing behind it every day, we decided that further documentation was needed. So we added some comments to the covers.
The photon accelerator:
The sparkle generator:
The supernova suppressor (important piece of security equipment):
For increased security: The teleborken current break.
And most important the HAL auxiliary unit:
Finally we plugged in the batteries and turned down the lights.
Since the sparkling effect does not show to well on still images, I made a video as well.
Published: 26.07.2013 16:57Plasma Birne - 07.12.2009
Vor ein paar Monaten kam ich auf dem Schrottplatz für kleines Geld in den Besitz mehrerer Zeilentrafos. Darunter auch ein altes Modell was noch keine Dioden integriert hat und deshalb Wechselspannung am Ausgang liefert. Erste Versuche mit meinem 2A Netzteil, einem Ne555 und einem Schalttransistor aus einem Verstärker lieferten eher mässige Ergebnisse. Die Ausgangsspannung war zwar definitiv größer 10kV, aber nicht viel. Mein Netzteil liefert bei vollen 2A in der Primärwicklung nur noch 5V. Ein Halogentrafo, ein Gleichrichter und zwei Glättelkos, aus einem alten PC-Netzteil, ergaben ein Netzteil mit 25A bei 16,4V Jetzt wird zwar der Transistor mangels ausreichend großem Kühler ziemlich heiß, aber die Ausgangsspannung ist, mit ungefähr 20-24kV, hoch genug für das berühmte Plasma in der Glühbirne.
Nicht zum Nachbau empfohlen, aber funktioniert. Ernsthaft die Hochspannung tut mindestens weh und kann im schlimmsten Fall zu schweren Verletzungen führen. Macht euere Hausaufgaben wenn ihr damit experimentieren wollt.
Published: 07.12.2009 20:44CNC-Fräse - 20.06.2009
Die Idee
Vor ein paar Monaten, besser gesagt in der letzten Schulwoche vor den Sommerferien 2008, wo man als Schüler sowieso nur noch Unsinn im Kopf hat kam mein Kumpel Robert mit der Idee zu mir eine lowcost CNC-fräse selbst zu bauen. Im Vorfeld hatten wir mal wieder diskutiert ob und wie man Ersatz und Tuningteile für unsere Modellhelis selbst machen könnte. Das Anfertigen auf einer CNC-Fräse war das nächstliegende, doch die wenigsten haben so etwas zu Hause im Wohnzimmer stehen. Also wurde beschlossen eine CNC-Fräse zu bauen.
Die Anfangsplanung
Ich hatte auch vorher schon ein paar mal mit dem Gedanken gespielt eine Fräse selbst zu bauen, deshalb kam mir sofort die Holz CNC von BlaueLed auf Roboternetz.de in den Sinn. Billig und einfach aufzubauen. Der Plan war eine Fräse nach dem Vorbild, auch in Holz. Allerdings wollte ich im Gegensatz zu BlaueLed die Motorsteuerung komplett selbst realisieren. Erstens ist das billiger als fertige Karten bei Pollin zu kaufen und zweitens wollte ich ja auch irgendwas selbst machen.
Die Elektronik
Zu Beginn der Sommerferien 2008 habe ich damit angefangen ein Layout für eine eigene Schrittmotorsteuerung mit L297 und L298 zu entwerfen. Als Basis dafür habe ich die Standard Application auf dem Datenblatt des L297 und die Hinweise im Roboternetz Wiki benutzt. Leider hatte ich in den Sommerferien recht wenig Zeit (3 Wochen Ferienjob, 2 Wochen Urlaub in Schweden, eine Woche Wacken), weshalb der erste Prototyp erst während der ersten Schulwochen fertig wurde.
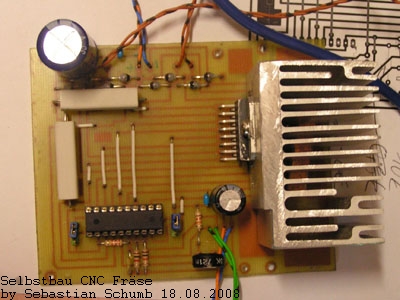
Wie man sehen kann ist die Platine noch alles andere als perfekt. Der Elko hängt etwas in der Luft und auch die Dioden sind leicht gequetscht. Außerdem sind die Kabel tödlich dünn für die 2A die meine Motoren ziehen. Aber jetzt mussten wir uns zunächst einmal um die Mechanik kümmern.
Während Roberts Arbeiten an der Mechanik sind dann bei mir die Hauptbestandteile der Steuerung entstanden. Ich habe die Steuerung in mehrere Module aufgeteilt die nacheinander gefertigt wurden. Der modulare Aufbau hat mehrer Vorteile: Erstens wenn ein Modul ausfällt muss man nicht gleich die ganze Steuerung tauschen. Zweitens wenn sich im Konzept eines Moduls ein Fehler eingeschlichen hat, muss ich nur ein Modul neu planen (mehrfach passiert). Drittens das herstellen kleinerer Platinen ist einfacher und weniger fehleranfällig. Hinter der ganze Elektronik steht ein ASG (aus Schrottteilen gebastelt)-PC (250mhz, 128mb, Win98) mit der kostenlosen Software NC-FRS.
Die m2c-Karte
Das Bild ist noch der erste Prototyp mit großen Transistoren. Diese wurden später durch wesentlich kleinere ersetzt. Diese Platine setzt die Signale der End- und Anfangsschalter und des Not-Aus-Schalters durch einfache Transistorschaltungen auf auf die Paralelle Schnittstelle der Pcs um. An jeden Schnistellenpin ist ein Pullup nach +5V wird ein Schalter ausgelöst zieht ein Transistor den Pin auf Masse. Die Platine ist übrigens im Toner direkt Verfahren entstanden, wie fast alle kleineren Platinen in diesem Projekt.
Der Not-Aus-Schalter
Eines der einzigen hardwareseitigen Bedienelemente an der Fräse. Wird der Schalter gedrückt gehen die grünen Leds aus und die roten leuchten auf. Außerdem geht ein Stop-Signal an die Software und die Stromversorgung der Motoren und des Fräsers wird unterbrochen. Die nötige Logik dazu sitzt auf der m2c-Karte und auf der Notausrelais-Karte. Die drei Leds am Rand der Platinen dienen dazu die Bewegungsrichtung der Motoren anzuzeigen. Die rote Kappe ist der Deckel einer Cola Flasche mit etwas Heißkleber auf dem Schalter befestigt.
Die c2m-Karte
Diese Karte ist das Gegenstück zur m2c-Karte. Sie setzt die Steuersignale vom Pc für die Motoren um. Das zentrale Bauteil ist ein SN74LS373. Über die 8 Latches wird das etwas unsaubere Signal der Schnittstelle auf saubere 5V-0V-Pegel gebracht, bevor es an die Motorendstufen geht. Für jeden Motor wird ein Takt und ein Richtungssignal übermittelt. Dadurch kann man alle Motoren mit nur 6 Schnittstellenpins steuern. Die Transistoren Schalten die Richtungsleds am Notaus.
Notausrelais-Karte
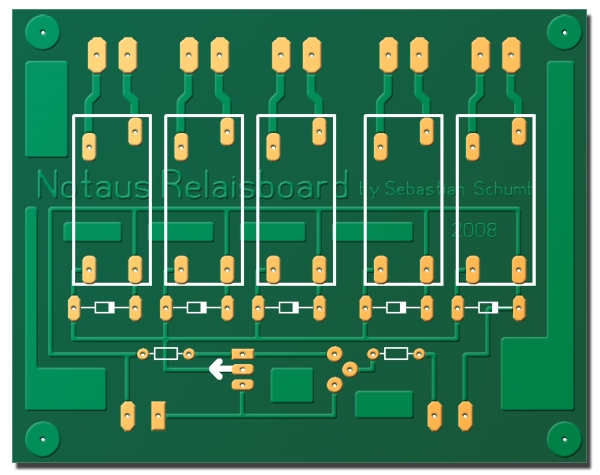
Diese Karte enthält 5 Relais die, wenn der Notausschalter gedrückt wird die Stromversorgung zu den Motorendstufen und zum Fräser unterbrechen. Geschaltet werden die Relais über einen starken Schalttransistor.
Motorsteurung Version 2.0
Nach dem das Drumherum einigermaßen stand konnte ich mich wieder an die eigentlichen Motorsteuerungen machen.
Auf der neuen Platine ist genug Platz für alle Teile und man kann die Betriebsmodi des L297 über Jumper setzen. Dafür passt sie jetzt nicht mehr auf eine halbe Eurokarte. Einen Mittlerweile mehrfach überarbeiteten Schaltplan gibt es hier.
Die Motoren
Da mittlerweile auch die Motoren von Pollin angekommen waren (5eu das Stück), konnte ich einen ersten Testlauf mit einem Motor machen. Ein Motor läuft mit 24V und zieht dann knapp 2A. Hier ein Bild mit allem zusammen aufgebaut und ein Bild von meiner Werkstatt.
Das Gehäuse
Als auch die Hilfsstromversorgung, ein einfaches Netzteil aus einem Trafo, Gleichrichter und 7805/7812, fertig war, gings ich daran alles möglichst kompakt unter zu bringen. Aus zwei MDF-Platten und 4 Gewindestangen habe ich einen zweistöckigen Aufbau gebaut, in dem die ganze Elektronik, bis auf die Motorendstufen untergebracht wird. Diese Sitzen möglichst nah an den Motoren und werden über geschirmte (Ethernet-)Kabel mit Signalen und Strom versorgt.
{{ lightbox(image="/electronics/cnc/control_all.jpg", , alt="Elektronikaufbau") }}
Auf der unteren Ebene befinden sich die Hilfsstromversorgung, die Notausrelais-Karte und ein Sicherungshalter, über den die Leitungen zu den Motorendstufen mit 2A abgesichert werden. Später wurde noch ein Spannugswandler 12V auf 9V dazumontiert, weil die Relais doch keine 12V auf Dauer vertragen. Die Gewindestangen sind einfach in die MDF-Platte geschraubt, man kann ohne Probleme Gewinde Platte schneiden. Auf der zweiten Ebene sind die c2m und m2c-Karte montiert. Über 5 9polige Sub-D Buchsen können die Motorendstufen, die Endschalter und der Notausschalter angeschlossen werden.
Elektroniktest
Abschließend gab es noch einen großen Test mit allen Motoren:
Der Test lief zu meiner vollsten Zufriedenheit, alles dreht wie es soll, nirgends steigt Rauch auf.
Die Stromversorgung der Motoren übernimmt ein fast neues Sitop Netzteil von Siemens, eine Dauerleihgabe einer großen deutschen IT und Elektronik Firma mit einem türkisen Logo.
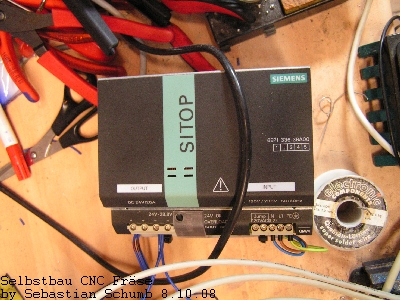
Die Mechanik
Während ich an der Elektronik gearbeitet habe hat sich Robert um die Mechanik gekümmert. Mein Vater hat uns freundlicherweise 6 paar Gleitschienen aus einem alten Serverrack organisiert, die mit einer relativ geringen Reibung (Kugellager) und mit noch weniger Spiel laufen. Diese sollten unsere Konstruktion die notwendige Beweglichkeit geben. Außerdem war Robert auch nicht untätig gewesen.
Er hatte es geschafft über Kevin, der einen Ferienjob bei der Firma Stabila in Annweiler hatte an knapp 14kg Aluprofile zu kommen. Bei Stabilia werden Wasserwaagen produziert, dafür waren auch unsere Profile gedacht gewesen, allerdings sitzen einige Bohrungen falsch, was die Profile zu Ausschuss macht. Die Profile sind für unsere zwecke ideal:
Sie haben eine große Wandstärke (versucht mal eine Wasserwaage zu verbiegen) und sind absolut gerade (erwartet man ja irgendwie von einer Wasserwaage). Vielen Dank noch mal an Kevin und die Firma Stabila. Robert der sich dem Aufbau der Mechanik befasst, ging gleich daran aus den Profilen den Rahmen unserer Fräse zu bauen.
Die Profile wurden zugeschnitten und auf eine recht unorthodoxe Art und Weise verschraubt: Es war ja ursprünglich eine Holzfräse aus MDF geplant. Deshalb lagen jetzt noch etliche MDF-Platten in der Werkstatt herum. Diese wurden auf die Innenmaße der der Profile gebracht und in deren Enden gesteckt nachdem die Schraubenlöcher durch die Profile gebohrt wurden. Danach kann man die Teile mit einfachen Spaxx-Schrauben durch die MDF-Platten in den Profilen verschrauben.
Endmontage und Tests 7.4.2009
Nach einer anstrengenden Woche in Roberts Werkstatt waren alle Motoren und Spindeln eingebaut. Es waren mehrere Anläufe und Konzepte für die Anbringung der Lager und der Motoren nötig. Aber jetzt läuft alles perfekt gerade und spielfrei. Die Motoren sitzen auf Roberts selbtsgeschnitzten Silikongummipuffern. Die Spindeln sind über selbstgedrehte Buchsen direkt an den Motoren angeflanscht. Am anderen Ende sitzen Kugellager in gedrehten PVC Scheiben, die mit Epoxy mit dem Rahmen verklebt wurden.
Anschließen gab es erste Tests mit Stift und Papier oder Dremel und Styropor.
EMC Linux
Die Kombo aus Win98 und NC-FRS erwies sich im Lauf der Zeit als anfällig für Abstürze.
Außerdem hatte NC-FRS viele tolle Rechtschreibfehler, wie z.B. "verfahrten" oder "Werzeuge"
und keine Unterstürzung für 3D-Fräsen.
Durch meinen Ferienjob bei Siemens konnte ich einen alten PC mit 1Ghz und 512mb Ram ergattern.
Eine alte Grafikkarte und eine Festplatte aus meiner Müll äh... Ersatzteilkiste machten den PC komplett.
Als Software kam für mich nur eine OpenSource Lösung in Frage. OpenSource hat den Vorteil, dass man die Software optimal an unsere Anwendung anpassen kann. Das Steuermodul des Heißnadleschneiders ist ein gutes Beispiel für solche Anpassungen. Außerdem hat OSS noch den für mich als armen Schüler/Student den Vorteil nichts zu kosten.
Beim Googeln stieß ich auf EMC-linux. EMC benutzt eine Realtime-Erweiterung für den Linux Kernel um eine graphische Bedienoberfläche über einen frei konfigurierbaren HAL mit IO-Hardware zu verbinden. Als Hardware können sowohl spezielle IO-Karten, als auch die Pins von parallele Schnittellen genutzt werden. Die Bedienoberfläche stellt dabei in der HAL sog. Pins bereit, die mandann über weitere Modulen (wie z.b. PWM-Generatoren oder logischen Verknüpfungen) mit den Pins der Schnittelle verbinden kann. Außerdem können eigene Module für die im Userspace laufen mit Python geschrieben werden. Dadurch kann man EMC für fast beliebige Anwendungen anpassen.
Da EMC auf Ubuntu basiert ließ es sich schnell und unkompliziert installieren. Nach dem Lesen der Manuals war die Konfiguration für unsere Hardware in einer halben Stunde erledigt.
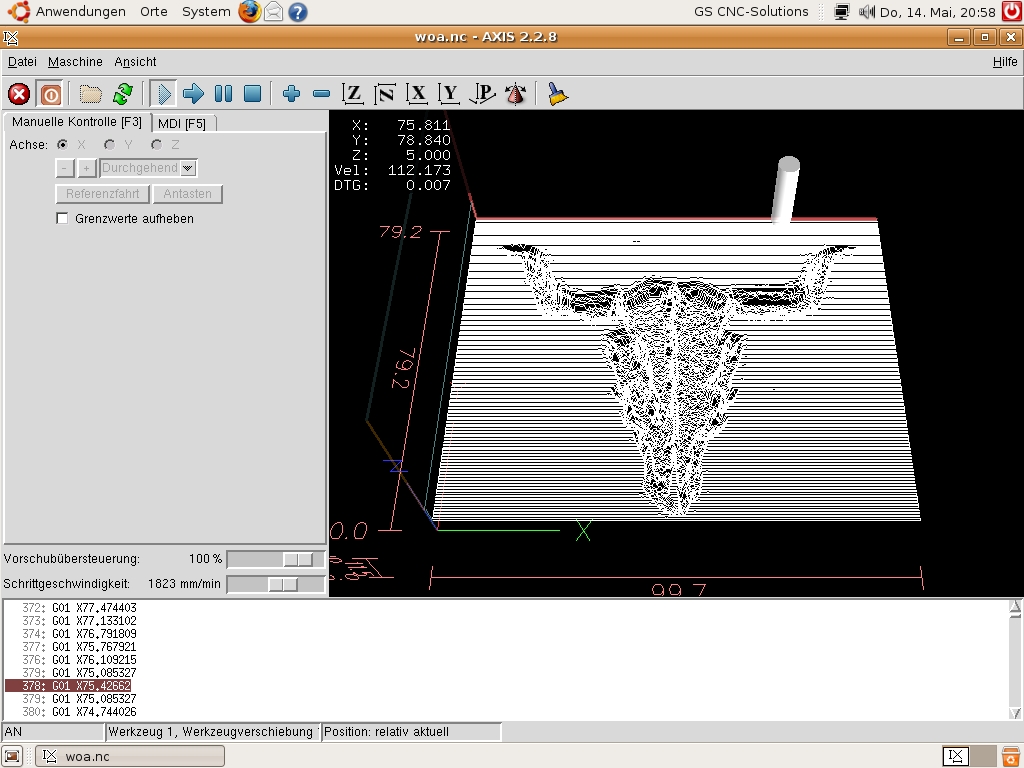
Anlässlich dieser Umstellung hatten wir auch Gelegenheit unsere Fräse am Linux Info Tag 2009 in Landau vorzustellen. Da wir dort wegen der Verschmutzung allerdings nichts Fräsen konnten musste ein sauberer Weg etwas mit unsere Fräse herzustellen. Deshalb habe ich ein Werkzeug für unsere Fräse entwickelt, das mit einer beheizten Aluminiumspitze Depron zerschneiden kann. Mit diesen Heißnadelschneider (als Analogie zum Heißdrahtschneider) haben wir vor Ort kleine Wurfgleiter aus Depron hergestellt.
Heißnadelschneider
Wer schon einmal Modellflugzeuge aus Depron gebaut hat, weiß wie nervig die vielen kleinen Schnippsel sind, die dabei anfallen. Die Lösung ist normalerweise das Schneiden mit einem heißen Draht. Allerdings lässt sich an unserer Portalfräse nur schwer ein Draht spannen.
Meine Lösung war eine beheizbare Nadel die ich auf meiner Drehbank aus Aluminium gedreht habe. Die Nadel wird in einen Alublock eingeschraubt, der mit einem Lastwiederstand beheizt wird.
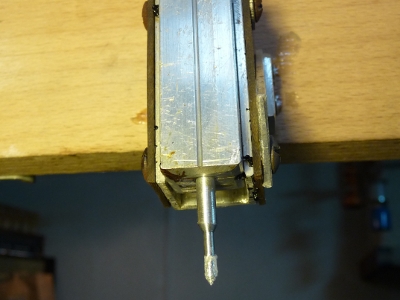
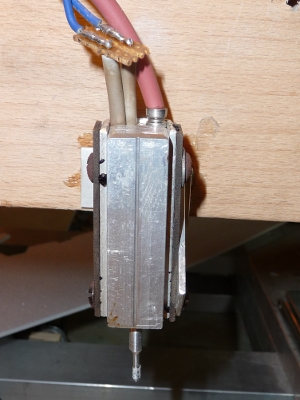
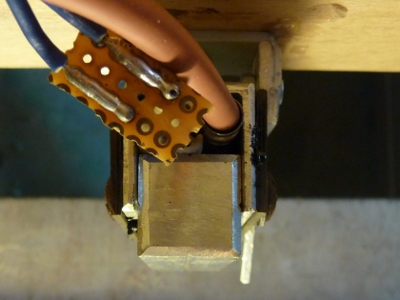
Ein U-Profil drückt den 10 Ohm 20Watt Zementwiderstand gegen einen Aluklotz. In dem Klotz ist ein M4 Gewinde, in das die gedrehte Spitze geschraubt wird.
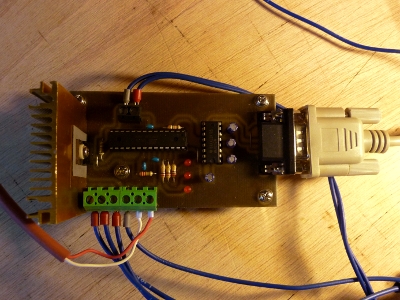
Gesteuert wird das ganze durch einen Controller aus einem ATmega8 mit PT1000 (ja etwas Overkill, war aber bei Pollin billig) der die Temperatur überwacht und ein MosFET was die Heizung schaltet. Über RS323 wird die Soll-Temperatur von einem EMC2 Modul gesetzt und der Ist-Wert ausgelesen. Das ganze ist dann voll in EMC2 integriert, z.b. wird gewartet bis die Temperatur passt, bevor ein Werkstück gekokelt wird. Außerdem gibt es ein PyVCP-Panel mit dem die Temperatur eingestellt und angezeigt wird. Geschnitten wir je nach Geschwindigkeit mit 180-220°C. Die fertigen Werkstücke weißen schöne glatten Kanten auf und mein hat keine Depronschnippsel an der Maschine kleben.
Published: 20.06.2009 15:32Facharbeit: Barometrischer Höhenmesser - 20.06.2009
So nach dem ich gestern endlich das Kolloquium zur meiner Facharbeit gehabt habe, kann ich meine Ergebnisse hier mal kurz vorstellen.
Los ging der ganze Spaß Anfang diese Jahr nach dem die Facharbeit angemeldet war. Offiziell hatte ich Zeit von Mitte Februar bis Ende April. Allerdings lagen in dieser Zeit zwei Blöcke Leistungskurs-Arbeiten, weshalb ich die Hauptarbeit komprimiert in den 3 Wochen Osterferien durchgezogen hab. (Inklusive ungezählter Nachtschichten)
Der Plan war einen barometrischen Höhenmesser zu bauen, der die Höhe in irgendeiner Form mitlogged. Als Einsatzszenario hatte ich dabei Modellflug und Raketenmodellbau im Blick.
Als erstes kamen die obligatorischen theoretischen Überlegungen. Was ist überhaupt Luftdruck ? Und wie hängt der von der Höhe ab. Für die Umrechnung wollte ich die internationale Höhenformel benutzen, deshalb musste ich mir diese dann selber herleiten.
Die eigentliche Umsetzung war in der Theorie dann doch eher einfach. Ein AVR sollte über eine Druckmessdose den Luftdruck messen, in eine Höhe umrechnen und anschließend als CSV Datei auf SD-Karte speichern. Klingt relativ simpel, aber die Tücke steckt da im Detail vor allem wenn man vorher noch nie einen AVR programmiert hat.
Gegen Ende wurde dann aber doch noch alles gerade so just in time fertig und ich denke das Ergebnis kann sich sehen lassen. Die Abweichungen vom Messwert zur Realität liegen gerade mal bei 5-15m.
Die Kritikpunkte die im Kolloquium angesprochen wurden waren:
- Die 'wischiwaschi' Herleitung der Höhenformel
- Die Beschreibung zum Quelltext ist zu oberflächlich
- Die Messreihe ist eher suboptimal und unzureichend ausgewertet
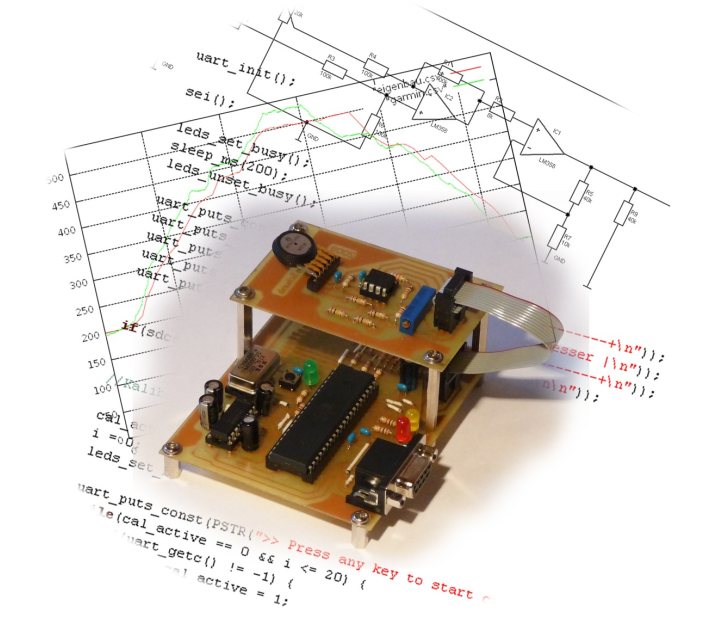
Die lange Version :
Published: 20.06.2009 15:32Stabilisiertes Netzteil - 10.01.2008
Ich hatte ein altes Labornetzteil, das mein Vater noch vor ewigen Zeiten selbst gebaut hat. Es hatte sowohl die Möglichkeit die Spannung (stufenlos), als auch die maximale Stromstärke (in Stufen) einzustellen. Außerdem war ein Sinusgenerator mit integriert. Das gute Stück hat mir jahrelang gute Dienste geleistet. Doch irgendwann hat die Spannungsregelung angefangen zu schwingen und der Sinusgenerator hat aufgehört.
So dann stand ich vor der Entscheidung, alte Reglung reparieren oder was komplett neues herein bauen. Da die alte Reglung (alles schön aus Transistoren aufgebaut) schon etwas outdatet war und ich noch ein LM317 zu Hand hatte hab ich mich für letzteres entschieden.
Hier mal kurz die Daten:
- Spannung: 0-25V ( sind der Einfachheit halber 1,25V-25V geworden)
- Strom: 10mA,150mA,500mA,1A und 2A
Der Widerstand R8 wäre eigentlich nicht nötig gewesen, aber da die Widerstände R3-R7 nicht so präzise sind, wie ich das gern hätte musste ich den Strom an der Stelle nochmal extra begrenzen, weil sonst der Transistor verdampft. Deshalb fließen jetzt auch immer ein paar mA mehr als ich eigentlich haben wollte, aber egal des basst scho ...
Noch ein paar Bilder :
Die Frontseite mit den Bedienelementen.
Die alten Innereien. Links Netzteil Rechts Sinusgenerator
Zwischenstand : Alles muss raus, um Platz zu schaffen für neue Möbel.
Stand Heute: Die neue Spannungsregelung ist eingebaut. (Platine ist selbst geätzt) Die Drähte die nach hinten aus dem Gehäuse raus gehen laufen zum LM317, der sitzt dort auf dem Monsterkühlkörper, wo früher mal ein Schalttransistor war. Das alte schwer gängige Poti mit dem die Spannung eingestellt wird ist durch ein 5-Gangpoti (also man kann es 5 mal um 360° drehen) ersetzt.
Sinusgenerator folgt noch. Im Hintergrund sieht man das Holzgehäuse wo alles wieder rein kommt.
Als nächstes werd ich einen Funktionsgenerator mit einem XR2206 bauen, der soll dann den alten Sinusgenerator ersetzen und mir dann auch noch Dreieck und Rechtecksignale liefern.
Published: 10.01.2008 16:42